How The 737 MAX Went Down
Boeing’s cost-cutting finally led to disaster
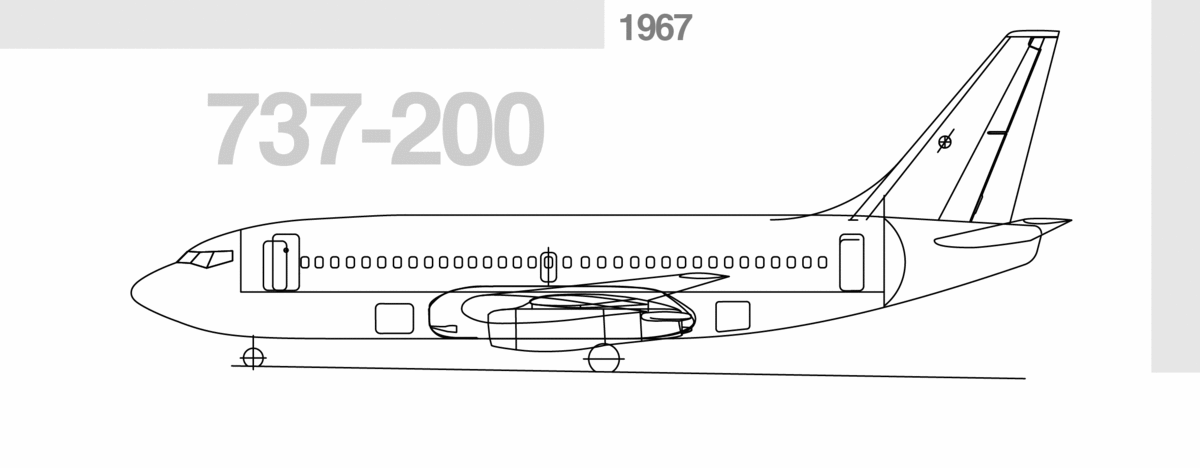
This is the final part of a series on Boeing’s culture crash. Part two was the nightmare of the 787 Dreamliner.
The 737 was an airframe designed in 1967 for just over 100 people. Over time it stretched to seat over 200, but it had one Achilles heel. In 1967, the ground staff just flung baggage into the plane, so it was built low to the ground. Modern engines, however, were more fuel-efficient, and thus bigger. Much bigger. This was the simple, physical problem with re-engining the 737. You couldn’t fit a 2010 engine under a 1967 wing.
Mike Bair and the President of Commercial Airplanes Jim Albaugh were aware of this and were in favour of an entirely new design. The Board, however, had learned the wrong lessons from the 787 debacles and was worried about a completely new design. Then Boeing’s only competitor, Airbus, forced their hand.
When Airbus was about to land American Airlines with a huge order for the A320 family, both the A320ceo and A320neo, Boeing’s hand was forced. Within 48 hours, Jim McNerney, Albaugh’s boss, made the decision to go forward with what would become the MAX. (Leeham News)
Again, this was a management decision which engineering just had to deal with. Airbus had re-engined their 1987 airframe so Boeing would re-engine their airframe from 1967. And they had to do it fast, cheap and good. It’s a law of project management that you can only get two out of three.
In hindsight, the 737NG was probably the ‘max’ that you could push that airframe to. For that plane, they went to the absurd lengths of squashing the engine casing, so much that it looks like someone dropped it.
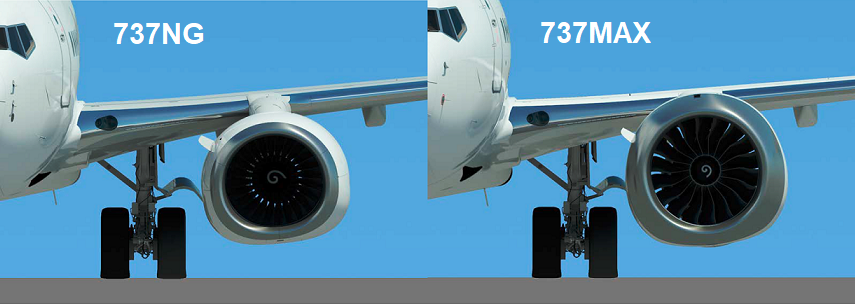
With the LEAP engine on the MAX, even squashing wasn’t enough. The engine had to be physically moved forward and upward on the wing. As you can see in the image above, it’s almost above the wing, and it’s huge. This changed the plane’s centre of gravity dramatically.
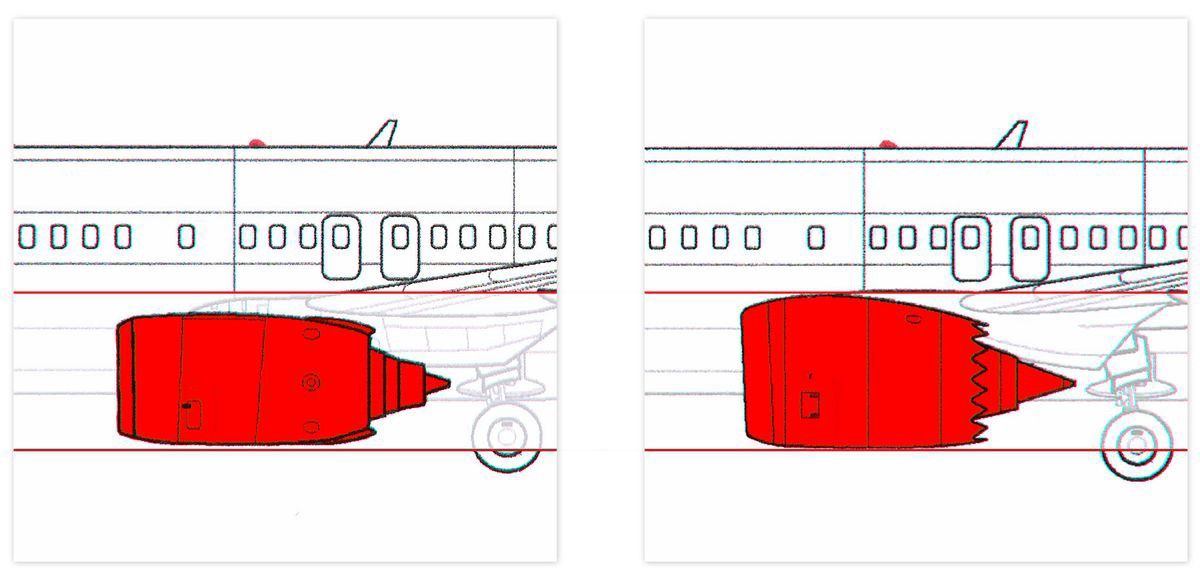
When Boeing started flying a scale model in a wind tunnel in 2012, the plane would pitch-up during certain manoeuvres. According to Eisenhower-era FAA regulations, when a pilot hits the gas, the plane cannot change pitch. This would be the equivalent of an aeroplane popping a wheelie, which is a very bad thing. Because the engine was further up, this is exactly what the 737 MAX did.
If we were in the mechanical era this would have been the end of the decision. The centre of gravity was simply wrong. Physics. New plane, new certification, new training. But alas, we were not in the mechanical era, or even the physical one. We were in the era of software engineers and financial engineering. They decided to hack it.
After failing to find a hardware solution to this problem, Boeing decided on software. This made it a hidden disaster for engineers, regulators, and ultimately 346 souls. At this point, however, it was already too late.
By the end of 2011, Boeing already had orders and commitments for 900 planes from 13 operators. Indeed, the MAX would go on to be Boeing’s best-selling model. The sales proposition (new engines, train on an iPad) was unbeatable and ultimately unrealistic. Boeing engineers had to just ‘make it work’.
At this point, the engineering challenge became less about building the best, safest plane and more about building something that could still be called a 737. A business decision led to an engineering problem that led to a regulatory problem. All of this just because they didn’t have enough inches under the wing.
Boeing came up with a solution, which I’ll describe in mechanical terms so you can see how crazy it is.
One sensor will detect if the plane is significantly pitching up. Then a mechanical arm will come out of the ceiling — over the pilot’s head — and push the control column down, hard. It will keep doing this every few seconds, as long as the sensor keeps firing until the plane hits the ground. This is MCAS, in a hardware form. There is no way any regulator would have approved this because it is insane.
This reality, however, was obscured under layers of software. Software that Boeing had mostly outsourced to $9 an hour coders in India. Software that was so complicated that the FAA could no longer regulate it and basically left it up to Boeing to test and certify. The software which they did not test and certify well. The software which ultimately killed 346 people.
The sad thing is that even this crazy software need not have been fatal. If pilots had been trained on it they could have had a fighting chance to control their plane before it violently lurched up and down before smashing into the ground at 600 kph. Boeing, however, had to make a 737 above all, and one that required only very basic retraining. So they just buried the existence of MCAS completely.
In 2017, Boeing’s chief technical pilot wrote to the FAA:
“Delete MCAS,” Forkner writes. “Recall, we decided we weren’t going to cover it in the FCOM [Flight Crew Operations Manual] or the CBT [Computer Based Training], since it’s way outside the normal operating envelope.” (Flight Global)
That is, any mention of this system that could crash the plane was deleted from all training documents. And Boeing was not unaware that this was a problem.
In those messages, Forkner and another employee, Patrik Gustavsson, talk about MCAS. Forkner says the system was “running rampant in the sim”, calling it “egregious”.
He adds, “So I basically lied to the regulators (unknowingly)”. (ibid)
Even after the first Lion Air crash in October 2018, Boeing defended their burial of the information.
“Since it operates in situations where the aircraft is under relatively high g load and near stall, a pilot should never see the operation of MCAS,” read a Q&A distributed to Southwest Airlines.
In reality, however, at least three flight crews did see MCAS in operation. And for two of them, and all souls on board, it was fatal. And terrifying.
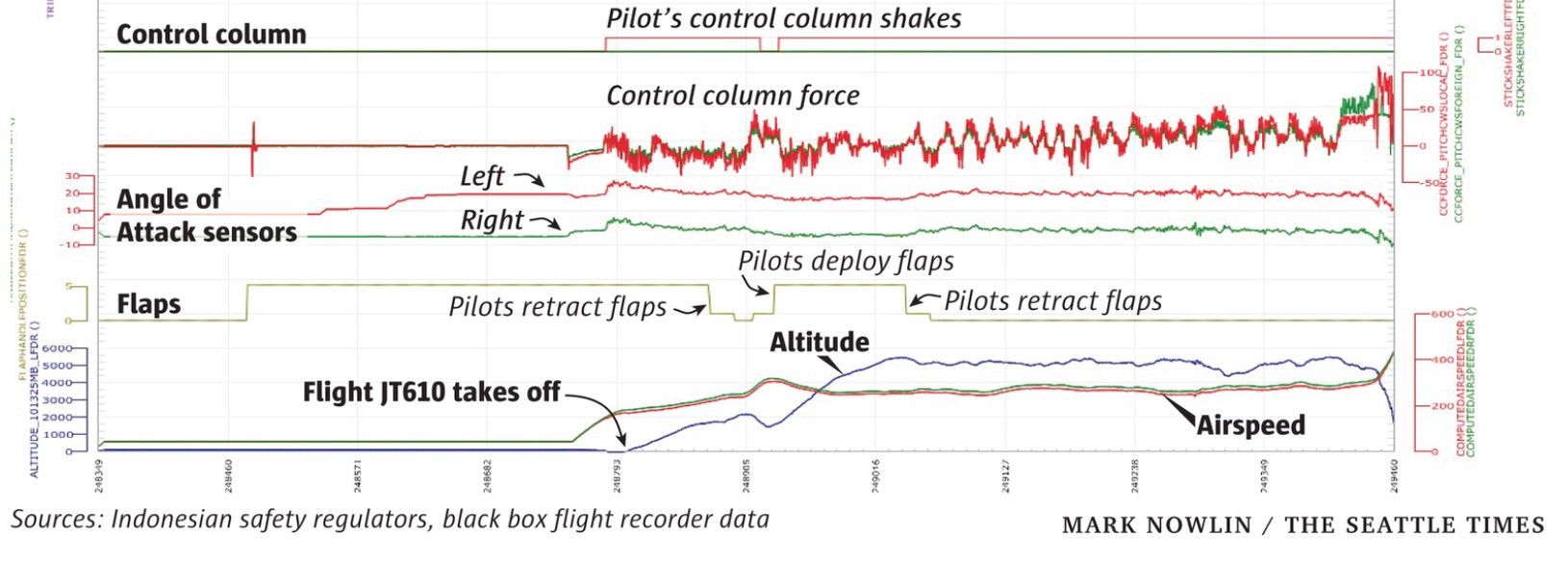
As you can see from the black box data from Lion Air JT610, the pilots are literally wrestling with the control column for 10 minutes, trying to pull the plane up 26 times. Finally, they lose, and the flight accelerates into the ground. It would have been absolute horror for everyone on board.
The Culture Crash
So how was this problem cultural?
Well, Boeing’s post-1997 cost-cutting drive had changed its engineering culture. The Dreamliner debacle had resulted in them outsourcing much of their engineering brain. Then with the 737 MAX, it finally led to an engineering disaster.
By the time of the 737 MAX, the board was scared of new plane lines and hundreds of years of experience had been laid off. When your ultimate concern is RONA, making more money off an old asset (the 737) seems like a good idea, even if it is an engineering impossibility. Then you sell aeroplanes without testing them, disaster becomes fate.
Finally, over a year after the first crash, Boeing has laid off its CEO and replaced them with… someone else from the same board. Someone who approved the same bad decisions and dangerous company culture. It simply doesn’t address the root cause.
If Muilenburg deserves to go, so does Greg Smith, the Chief Financial Officer and Executive Vice President, Enterprise Performance & Strategy.
The emphasis on cost control, which have become part of the focus of the MAX development, emanates from Smith. The strategy for new products ultimately falls under Smith, who vehemently opposes investment in the New Midmarket Airplane.
If these two deserve to go, so do the Board of Directors.
It’s the Board of Directors who set the shareholders’ value policy that Muilenburg carries out. (Leeham News)
As countless people from Dr L.J. Hart-Smith to Stan Sorscher to striking engineers had warned, the Boeing culture shift from engineering to financial engineering was disastrous. It allowed for short-term gains but now threatens the century-old company’s very existence. Most importantly, it has killed 346 souls, people who spent their last moments in abject, helpless terror.
As Scott Hamilton writes, in the face of this decades-long disaster, more than half of the board deserves to go.
Those long-serving Board members who were there at the beginning of the MAX program launch should be on the list to go.
This list includes lead director David Calhoun (2009); Arthur Collins (2007); Adm. Edmund Giambastiani (Ret.) (2009); Lawrence Kellner (2011); Ed Liddy (2010); Susan Schwab (2010); Ron Williams (2010); and Mike Zafirovski (2004). This is eight of the 13 members, which includes Muilenburg (2015).
Has Boeing taken this accountability? Not yet. The culture of failing up while planes go down continues.
Outgoing CEO Muilenburg is set to walk away with more of a golden parachute($60 million) than the total set aside for victims ($50 million). David Calhoun has been elevated from his failure as a board member to CEO. Calhoun has a major in accounting and experience at GE and in private equity. This is hardly a culture shift.
The current board has no engineers and remains mostly non-technical people with bachelor’s degrees and MBAs. It is still full of the GE and private equity types that led to this disastrous strategy in the first place. This is just business as usual.
Boeing today remains a financial engineering company, not an engineering company. It went from a company that made planes and money to a company that made money and planes. That change in focus is simply not acceptable for a company that carries human lives at great scale and speed. And it shouldn’t be acceptable to shareholders.
There is no engineering fix for the 737 MAX and the problems that led up to it. Boeing’s culture crashed before its planes did, and is that culture that needs to be remade again for the company to fly. Until then, the company has danger designed-in. It’s unsafe at any speed.
This is part three of a three-part series. Here’s the rest.
Part One
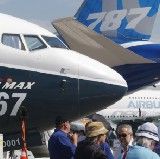
Part Two
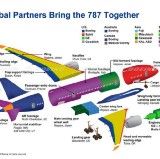